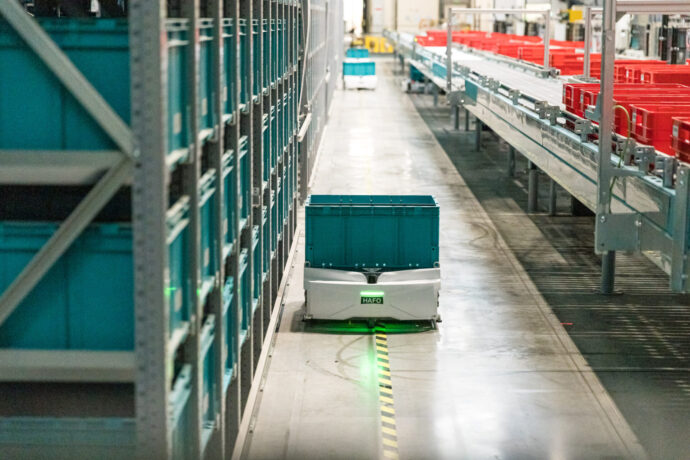
Industry
Share
Find out why CEVA Logistics, a global 3PL leader, turned to Exotec for the third time to drive warehouse transformation with agile AS/RS automation.
About CEVA Logistics
CEVA Logistics, a global leader in the 3PL sector based in Marseille, offers comprehensive supply chain solutions worldwide. With a presence in 170 countries and nearly 110,000 employees across 1,300 sites, the company specializes in contract logistics and air, sea, and land transport.
To address future customer needs for supply chain innovation and modernization, CEVA Logistics partners with trusted experts like Exotec. Our focus on supply chain optimization, especially robotic intralogistics solutions, aligns with their commitment to advancing logistics capabilities.
The Challenge
The 3PL market is projected to grow by approximately 9% from 2022 to 2031, driven by increased manufacturing and retail activities necessitating optimized supply chains. Despite this growth, the sector has faced challenges including labor shortages and rising property costs in recent years. CEVA Logistics, like others in the industry, also grapples with maintaining warehouse capacity and performance amidst their customer’s peak sales periods.
In this competitive landscape, CEVA Logistics relies on innovation to maintain its edge. Moreover, the company is dedicated to sustainable development, striving to automate logistics warehouses in an environmentally responsible manner.
In summary, the main challenges facing CEVA Logistics are:
- Absorbing diverse customer sectors while maximizing flexibility
- Meeting sustainable development objectives
- Increasing storage capacity amidst a scarcity of logistics real estate
The Skypod System Solution
CEVA Logistics previously partnered with Exotec to upgrade three of their logistics facilities in the Netherlands and United States, leveraging Exotec’s Skypod® system for improved order fulfillment productivity. The benefits to CEVA Logistics include:
Game-Changing Performance
- Efficiently managing urgent orders with the ability to retrieve any ordered item in the system within just two minutes
- high-density storage racks spanning the warehouse’s full height
- System dimensioned for several phases of future growth with the ability to add robots within minutes, stations within days, and storage racks within weeks with minimal interruption to ongoing operations
Achieving Sustainable Development Objectives
- Lightweight, battery-powered robots consume relatively low energy, contributing to the company’s sustainability objectives
- Solar-powered warehouses at CEVA Logistics significantly reduce the carbon footprint of these logistics sites
“At CEVA, our culture drives us to seek innovative solutions to better serve our customers, and the Skypod solution offers significant value in warehouse automation. With our strong commitment to responsive logistics, our customers expect a high level of service, efficiency and agility in our operations. The implementation of Exotec’s solution, among others, enables us to continue to create value alongside our customers.”
Yuri Bannier, Automation Manager at CEVA Logistics
Related Case Studies
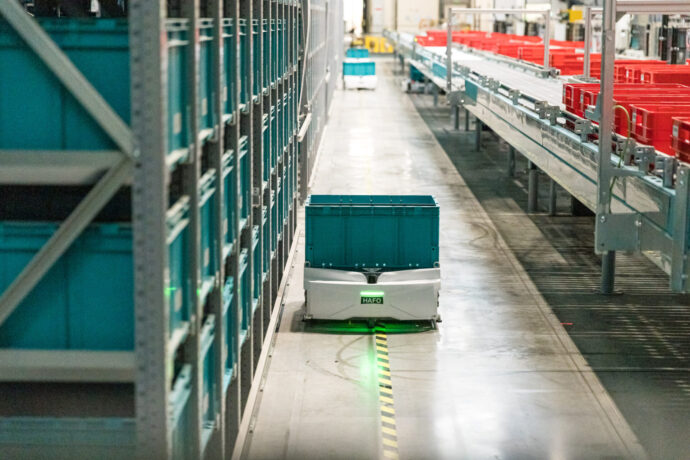
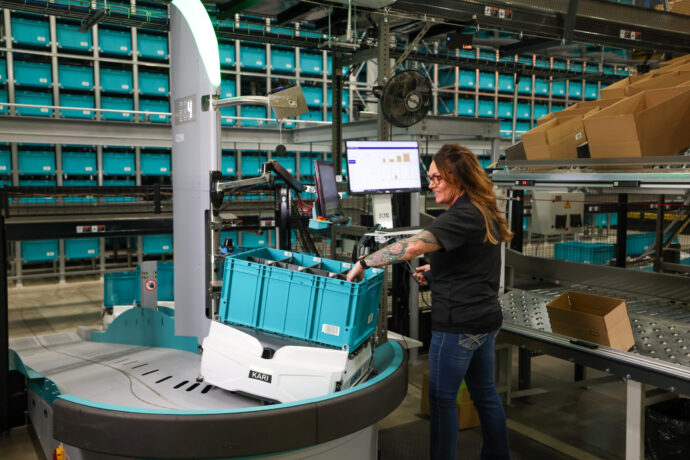
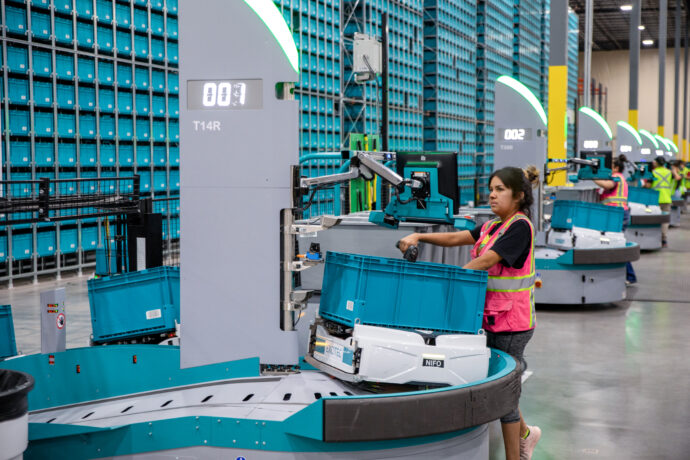