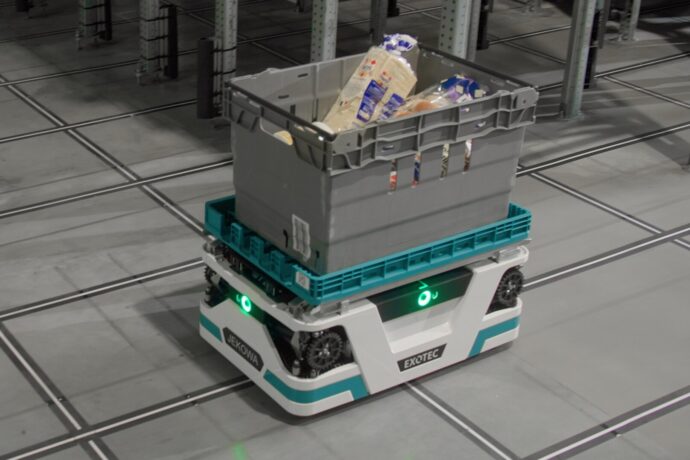
E.Leclerc – Case Study
Transformer l’expérience client avec le système Skypod® nouvelle génération
Learn how LACROIX Group’s Electronics division transformed its warehouse operations with the Exotec® Skypod® system. This change boosted productivity sevenfold, and optimized warehouse space, all while ensuring a seamless and swift transition to a state-of-the-art facility.
LACROIX Group is an international leader in technology equipment, offering innovative, connected, and secure solutions to enhance the management of road, water, and energy infrastructures. We had the privilege of collaborating with their electronics division, which ranks among the top 50 electronics manufacturing services globally. This division provides comprehensive services, from design to production, for sectors including automotive, industrial, smart homes and buildings, aerospace and defense, and healthcare.
Previously housed in an aging industrial building in Maine-et-Loire, France, LACROIX’s Electronics division made a strategic move in 2022 to a state-of-the-art facility in Beaupréau. The new facility was designed with a strong focus on industrial, social, and environmental innovation.
The primary goal of this relocation, where Exotec played a pivotal role, was to improve the reliability and efficiency of storing and preparing electronic components, as well as various plastic and metal parts, totaling over 4,000 different items. These components are essential for the production of embedded systems and other connected devices for LACROIX’s customers. The central ‘store’ where these parts are housed is a critical hub for the company’s operations. Any disruption, whether in throughput or precise inventory management, can have far-reaching effects on the entire production process.
The relocation process aimed at minimizing downtime and ensuring a swift resumption of business activities. “We could only stop our equipment for a week,” explains Claude Bourget, Manager of the Beaupréau site and of LACROIX’s Electronics division. And when it came to restarting, the promise was indeed there: “It worked from day one, it was plug-and-play, and we hardly had any fine-tuning phase.”
Robots | Picking Stations | Replenishment Stations | Bins | Bins/Hour | Rack Height | System Footprint |
---|---|---|---|---|---|---|
7 | 1 | 1 | 9,100 | 175 | 9 m (29 ft) | 430 m2 (4,625 ft2) |
Game-Changing Performance
“We’ve virtually eradicated non-value-added operations in the warehouse, allowing us to reallocate our teams to more engaging tasks. Undoubtedly, this change brings joy to his staff as well.”
Transformer l’expérience client avec le système Skypod® nouvelle génération