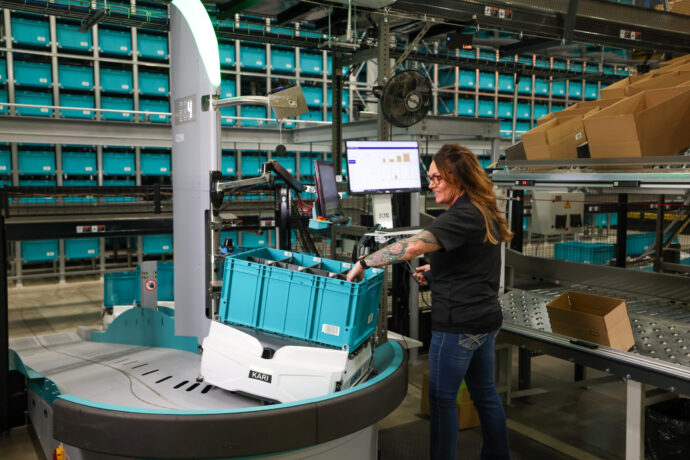
Industry
Share
Company Background
This technology repair company’s receiving center collects damaged, returned, and traded-in electronic devices including cell phones, tablets, and wearable devices from hundreds of store locations across the United States. These devices are refurbished, graded, stored, and subsequently dispatched to manufacturers across the country for resale.
The Challenge
Manually storing and picking inventory from shelves posed a significant obstacle to the operational efficiency of this electronics repair and resell giant. The labor-intensive process was ill-equipped for achieving sustained success with their just-in-time inventory management strategy. A lack of precise insight into the quantity and diversity of SKUs that would be arriving at the warehouse from hundreds of store locations across the country added to this challenge. Consequently, the company faced difficulties in predicting and maintaining the optimal number of warehouse employees needed to process goods.
Managing storage space posed an ongoing challenge for the company, given its proactive pursuit of acquisition opportunities and the constant expansion of devices it supports. Striking a delicate balance between stocking a diverse range of SKUs while avoiding both stockouts and overstocking was imperative, but made challenging due to the inefficient utilization of warehouse storage space and lack of efficient automation to streamline the process of storing and retrieving goods.
Furthermore, the inventory included delicate electronic devices like cell phones, tablets, and other items with fragile screens and components. To overcome these challenges and optimize their operations, the implementation of a highly efficient and scalable goods-to-person system became an urgent necessity.
The Skypod System Solution
Robots | Picking Stations | Replenishment Stations | Storage Bins | Bins/Hour | Rack Height | System Footprint |
---|---|---|---|---|---|---|
16 | 3 | 1 | 22,230 | 396 | 27.5 ft (8.4 m) | 13,422 ft2 (1,247 m2) |
System Integrated by Hy-Tek Intralogistics
Key Results
Game-Changing Performance
- Productivity increased by 5x with four picking stations capable of processing more than 350 lines per hour with just three employees
- Increased storage density by 5x by reducing inventory rack footprint from 26,500 ft2 (2,460m2) to 13,300ft2 (1,235m2)
- Ability to access any SKU in the system within two minutes without damaging fragile goods
- Automated storage of goods with bin interface capable of inducting more than 800 items per hour
- Transitioned large segment of labor to more value-add tasks such as grading inbound devices
- Seamless integration with additional automation within the warehouse
Related Case Studies
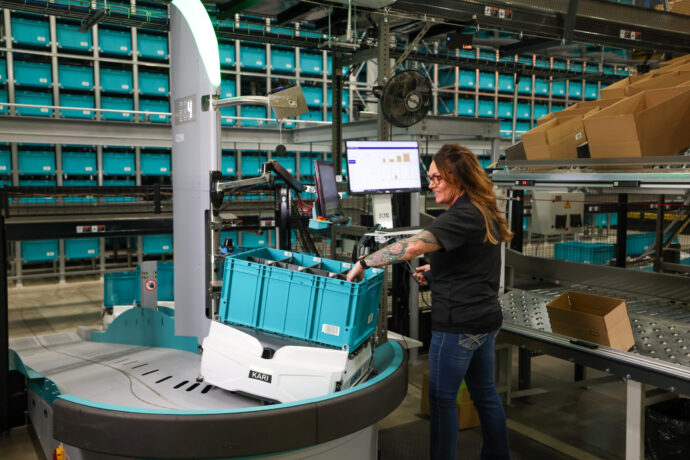
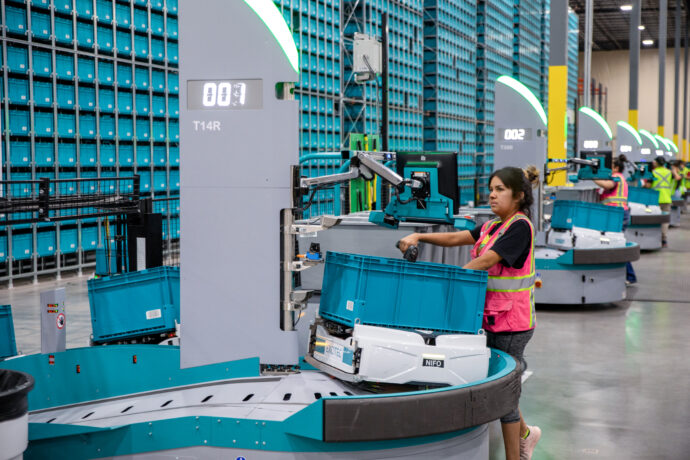
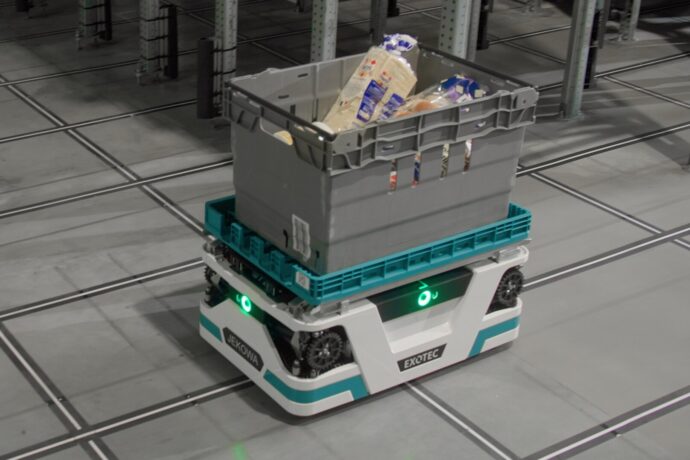
E.Leclerc – Case Study
Transformer l’expérience client avec le système Skypod® nouvelle génération