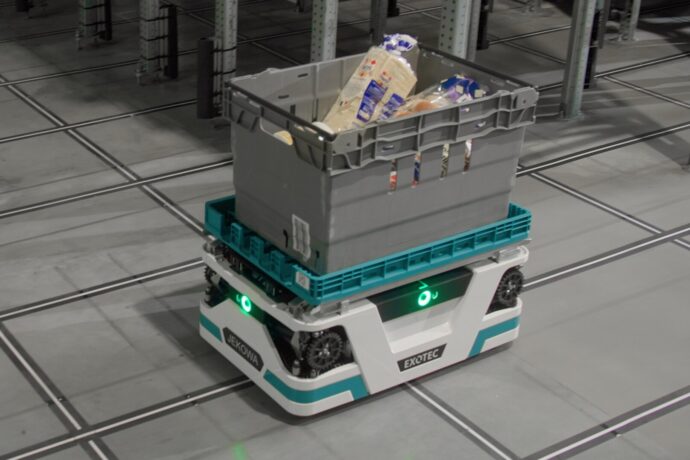
E.Leclerc Reinvents Drive-Through Fulfillment — 70% Faster, 50% More Orders
Transformer l’expérience client avec le système Skypod® nouvelle génération
Discover how bioMérieux simplified complex healthcare logistics — where every second counts — by integrating the Exotec Skypod system for faster, more precise operations.
Founded in 1963, bioMérieux is a global leader in in vitro diagnostics, offering systems, reagents, software, and services for both clinical and industrial applications.
With core technologies in microbiology, immunoassays, and molecular biology, bioMérieux operates in 45 countries and distributes products in over 160.
Its global logistics network is anchored by two International Distribution Centers in France and the U.S., which handle storage, order prep, and shipping.
With global demand for diagnostic solutions on the rise, bioMérieux reported rapid sales growth in the first half of 2024, prompting the need for a major logistics upgrade. The company sought to modernize its Saint-Vulbas International Distribution Center to ship up to 5,000 parcels and 400 pallets per day. Key challenges included:
Robots | Picking Stations | Replenishment Stations | Bins | Bins/Hour | Rack Height | System Footprint |
---|---|---|---|---|---|---|
12 | 2 | 1 | 8,000 | 300 | 9 m (29.5 ft) | 675 m2 (7,265 ft2) |
Boosting Productivity & Throughput
Enhancing Flexibility Within a Constrained Facility
Advancing Environmental & Packaging Efficiency
“The strength of the Skypod system is that it has allowed us to invest in the number of robots we need today, not the number of robots we will need tomorrow.”
– Frank Reverdy, IDC 2040 Project Director at bioMérieux
Transformer l’expérience client avec le système Skypod® nouvelle génération
Our retail experience at the service of a European leader
Delivering Seamless End-to-End Order Fulfillment